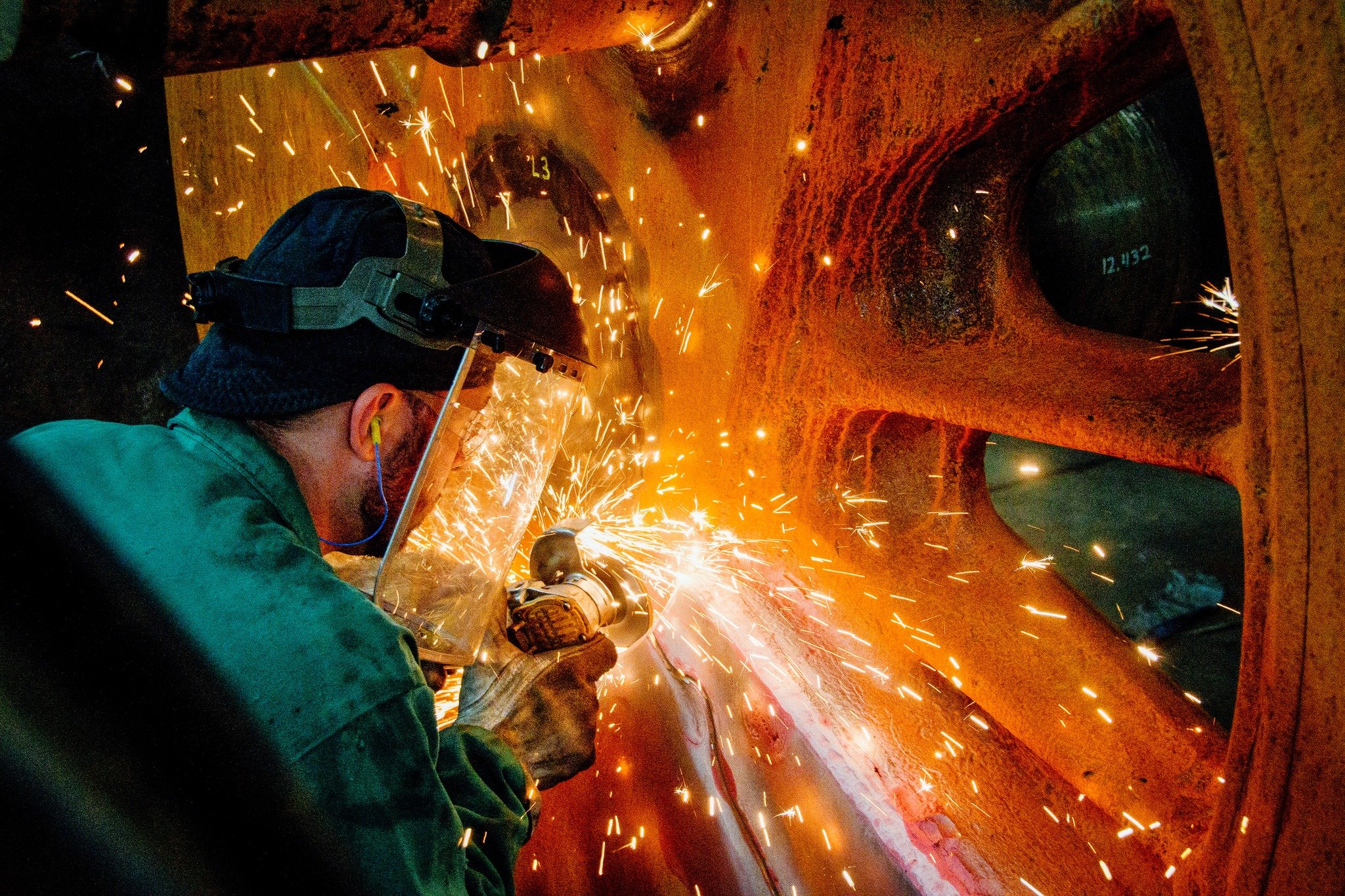
News

FMW Solutions Completes Restoration of Locomotive in Abbeville, Alabama
Over eight months, the FMW Solutions team completed disassembly and sandblasting of the steam locomotive, fabricated new parts, repaired and reinstalled appliances and rods, rebuilt the cab, restored the bell and headlight, and completed an extensive locomotive cosmetic restoration.

FMW Vice President Recognized with Historic Preservation Medal
Steam locomotive contractor FMW Solutions and Shane Meador has been honored with the Historic Preservation Recognition Medal for his exemplary leadership and contributions to the preservation of American railroad heritage.
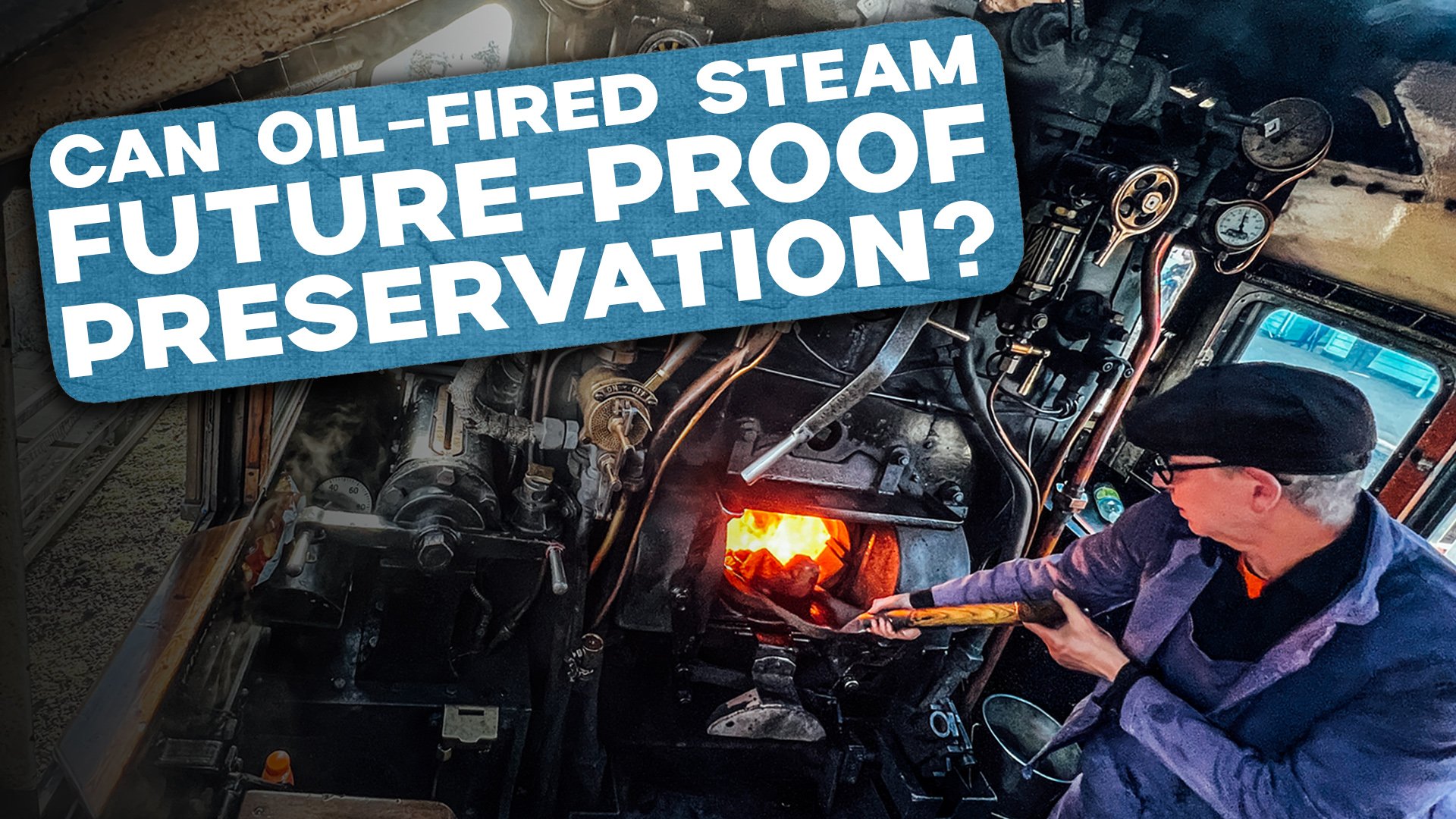
Converting Coal Fired Steam Locomotives to Oil
To future-proof rail preservation, FMW Solutions will convert a historic steam locomotive from burning coal to oil as part of the first full-size steam locomotive conversion project in the U.K. since the end of steam. Learn how this work will contribute to cost savings, labor savings, and lessen greenhouse emissions for an important heritage attraction.
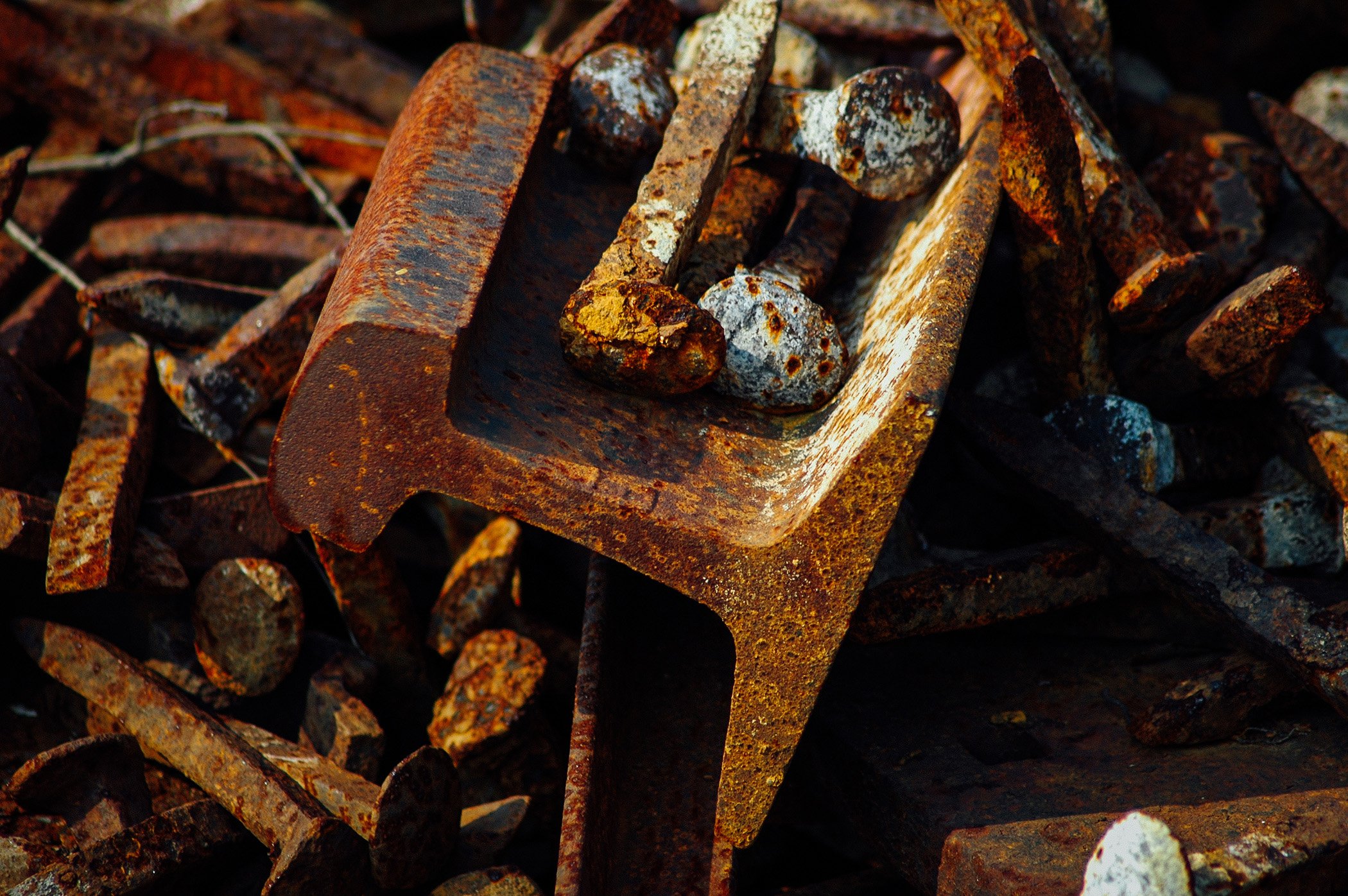
A Railroader's Guide to CRISI, Grant Writing, and Funding For Infrastructure Projects
Applying for a CRISI grant or funding for your railroad infrastructure project? Learn more about the opportunities for your rail efforts, including intercity passenger rail, freight rail, intermodal projects, and transit-oriented developments.
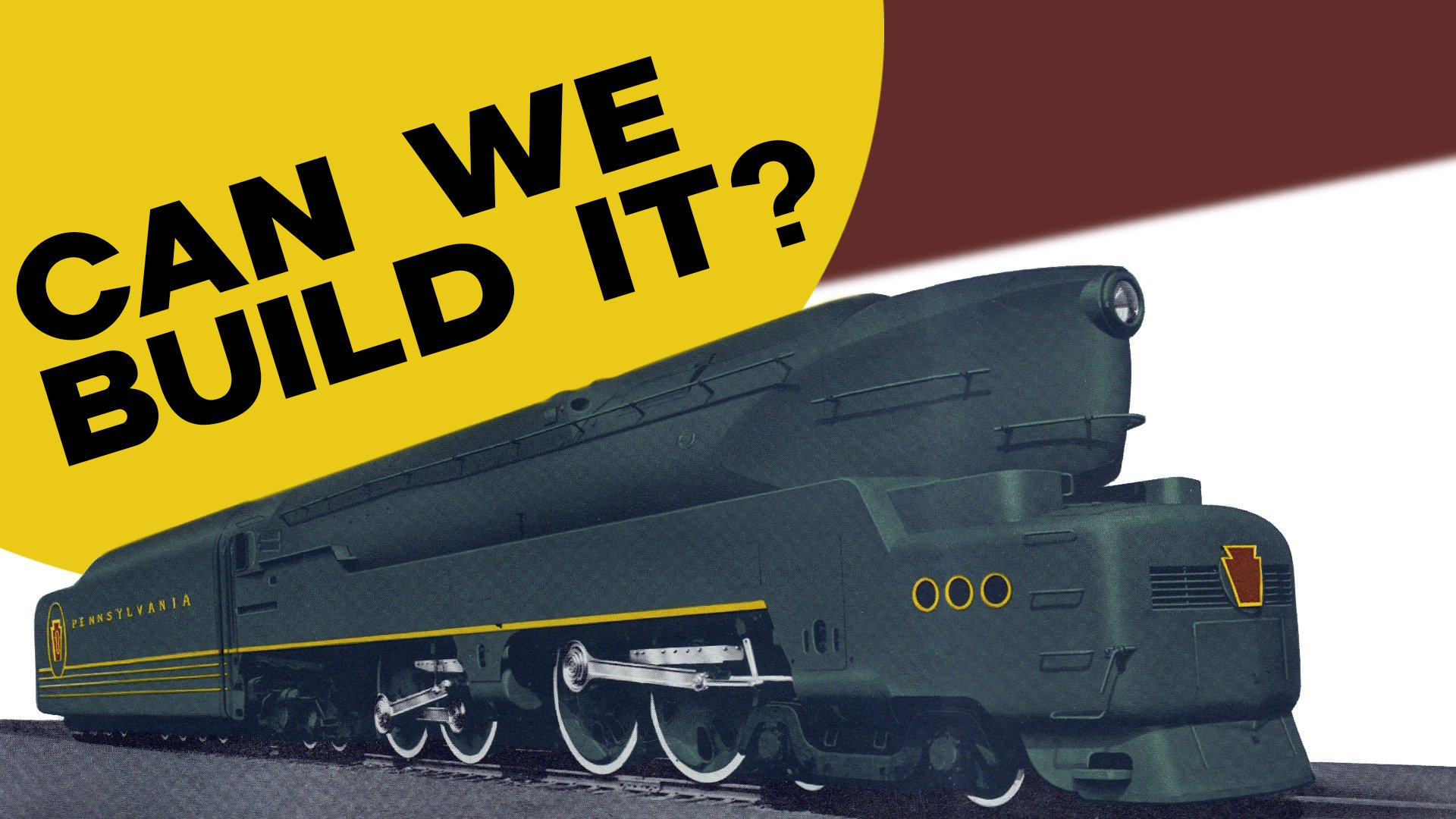
Can We Build a New Mainline Steam Locomotive?
Can we build a new mainline steam locomotive in the United States? Join our steam restoration, repair, and engineering experts for the answer.

Restoration of Oldest Surviving Electro-Motive Locomotive Begins
The Mid-Continent Railway Museum is embarking on the full operational restoration of Great Northern No. 2313 with the diesel locomotive and EMD repair expertise of FMW Solutions.
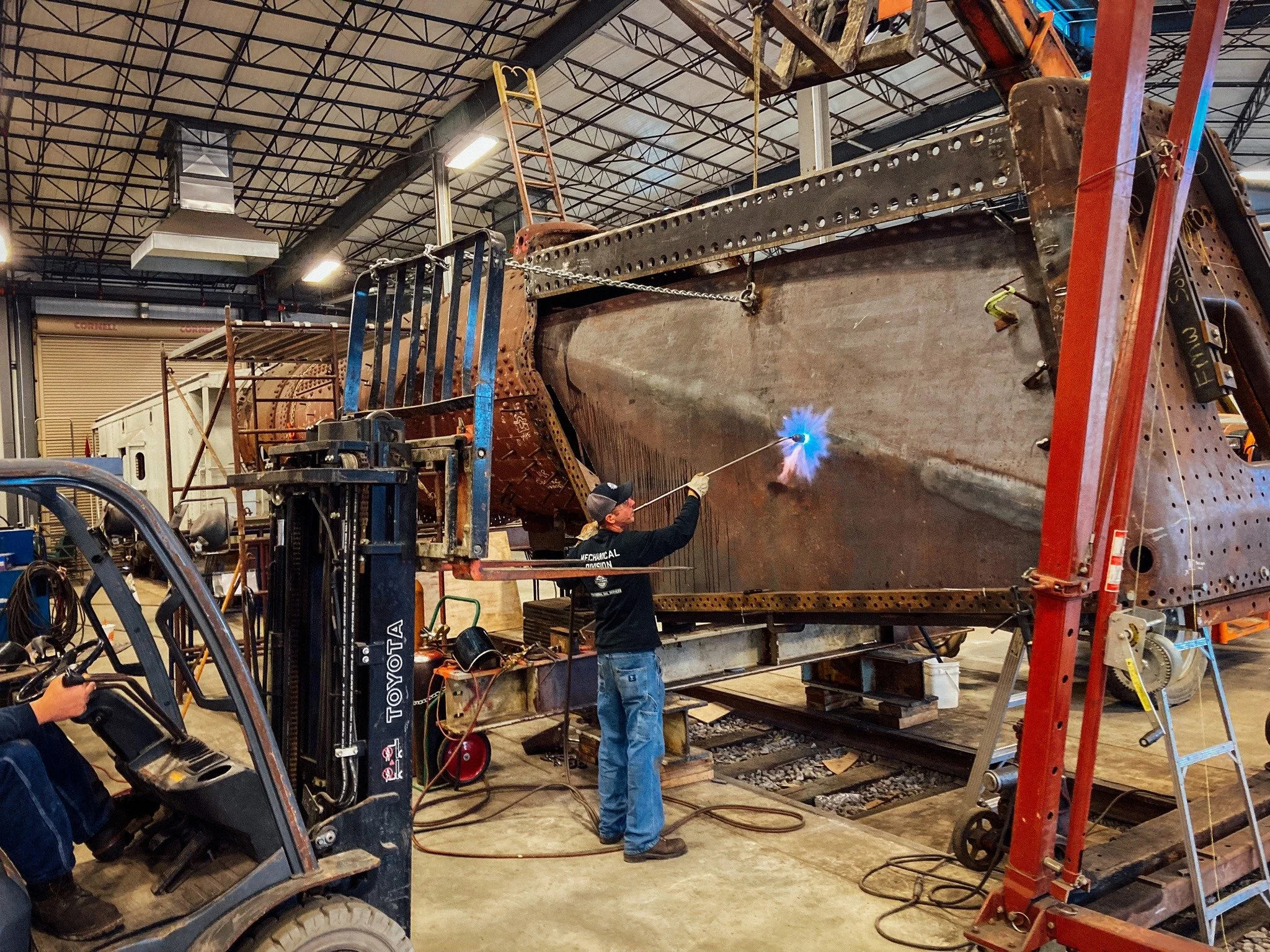
Steam Locomotive Assessment | Restoration Roundtable with Pennsylvania Raliroad No. 1361
The restoration of steam locomotive K4 No. 1361 is a thirty-year undertaking that has seen multiple project managers, with considerable work completed. However, there is still much to be done. The latest boiler studies and engineering work revealed some of the following.
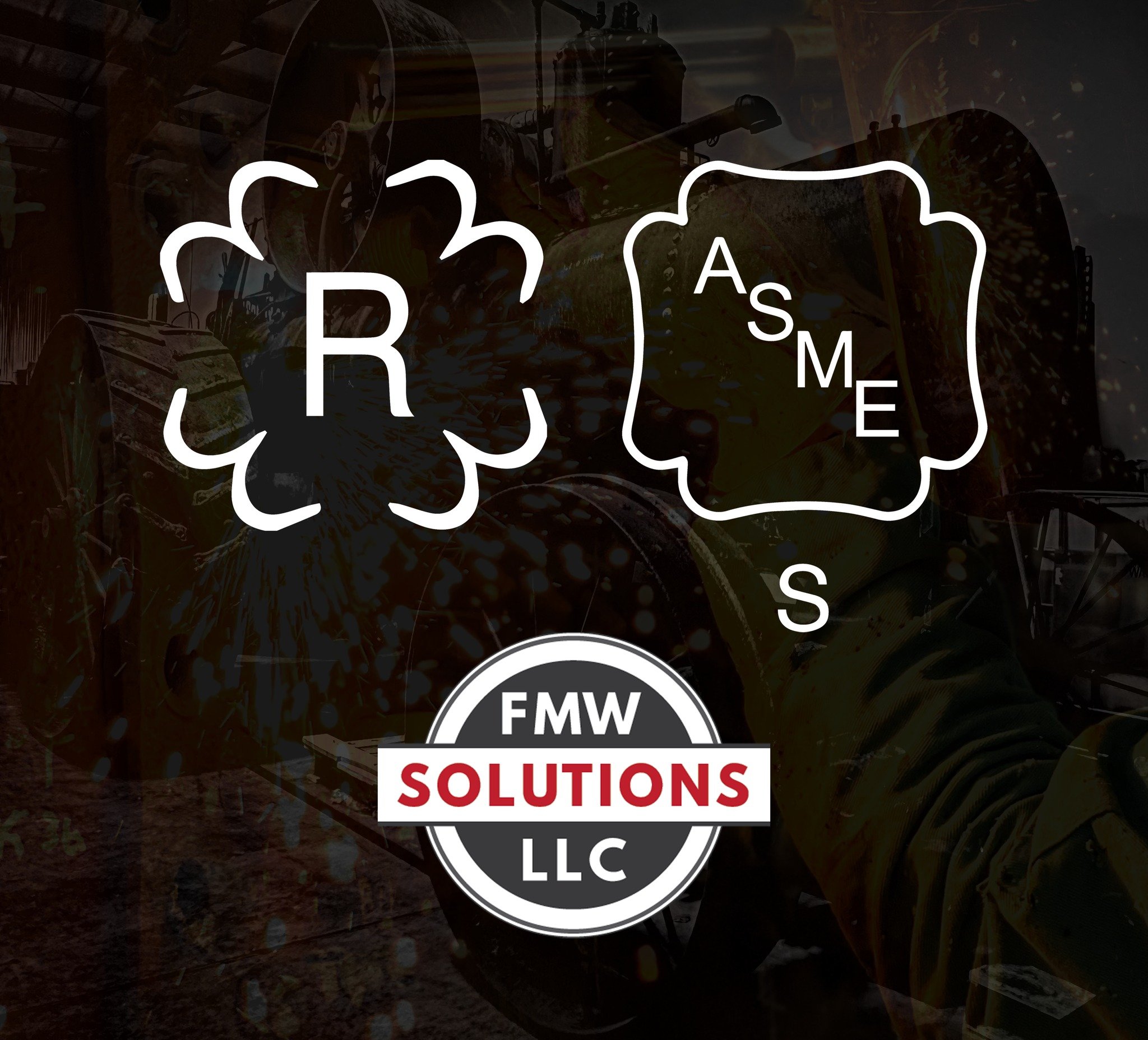
FMW Solutions earns ASME "S Stamp" and NBIC "R Stamp" Certifications for Boiler Repair
FMW Solutions has received its ASME “S Stamp” and NBIC “R Stamp” Certifications. These two certifications enable the firm to complete the new fabrication and repair to “Code” regulated pressure vessels, including steam locomotives operating at theme parks and historic traction engines. FMW is now under contract to assist a steam heritage railroad and a steam traction engine owner with code work, utilizing these new certifications to aid those clients in operating, building, and restoring their historic boilers.
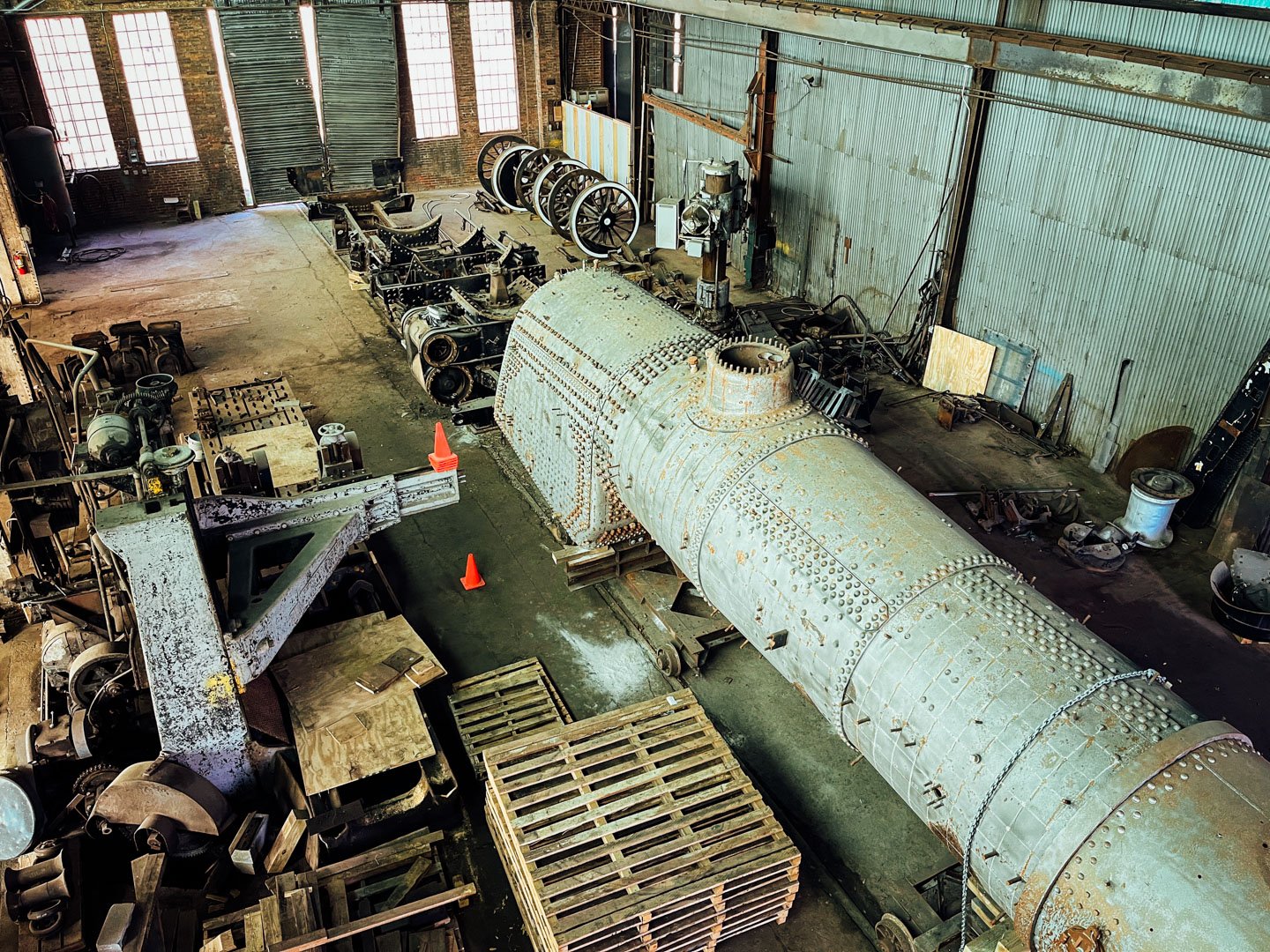
Steam Locomotive Restoration Making Tracks
Rail preservation firm FMW Solutions makes progress on historic steam locomotive restoration.
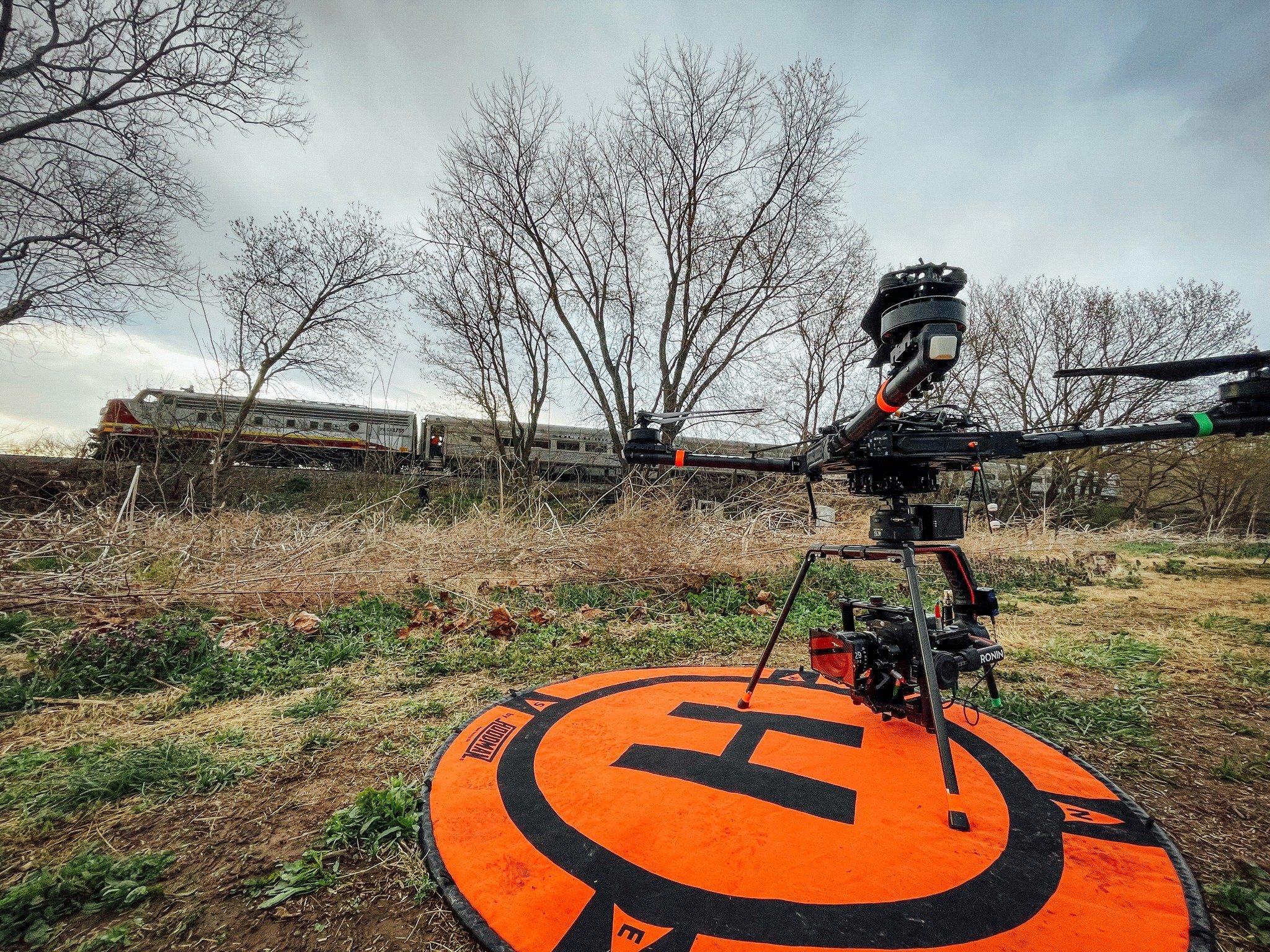