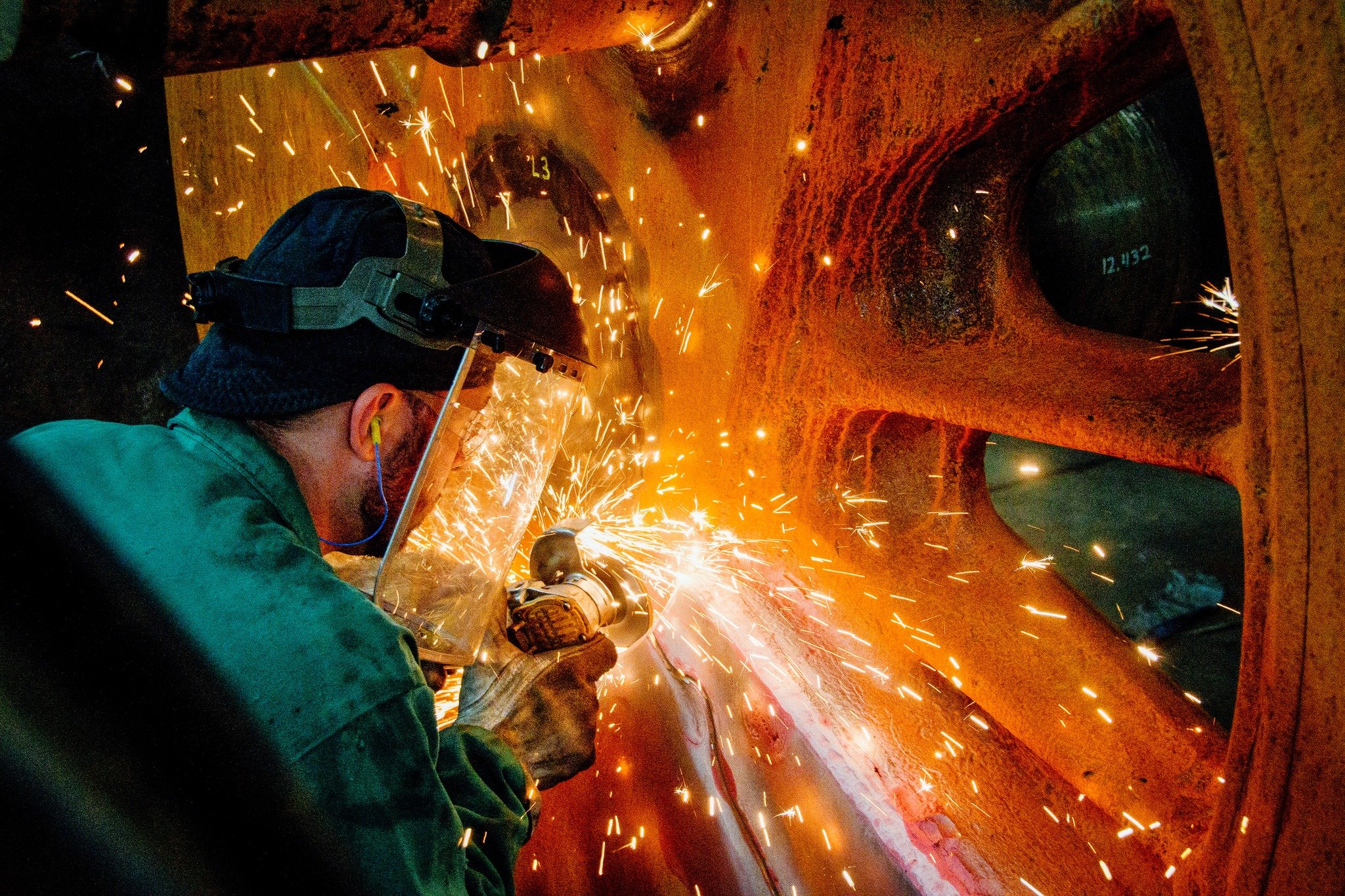
News
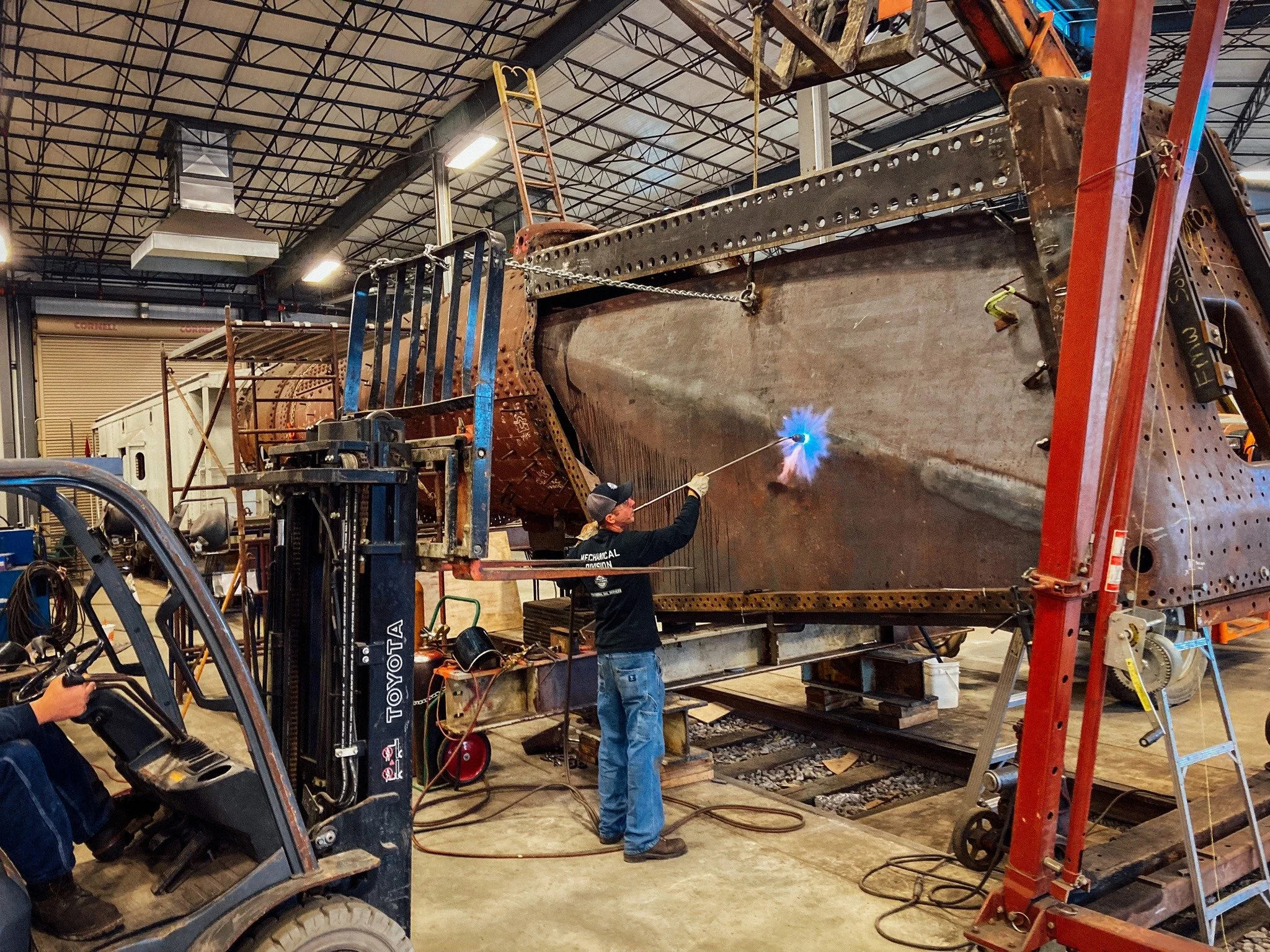
Steam Locomotive Assessment | Restoration Roundtable with Pennsylvania Raliroad No. 1361
The restoration of steam locomotive K4 No. 1361 is a thirty-year undertaking that has seen multiple project managers, with considerable work completed. However, there is still much to be done. The latest boiler studies and engineering work revealed some of the following.